Flexography Printing
Fast, Affordable, Quality Flexography Printing
CHOOSE THE SUPERIOR PRODUCT LABEL PRINTING COMPANY
- At Impression Label, we believe in offering high-quality product label printing and the printing of other products at a reasonable price. With flexography printing, or flexo, we can do just that. Whether you need to print labels, packaging materials, or folding cartons, we are the team you can trust to get the job done. Keep reading to learn more about flexography printing at Impression Label and contact us today to start your project!
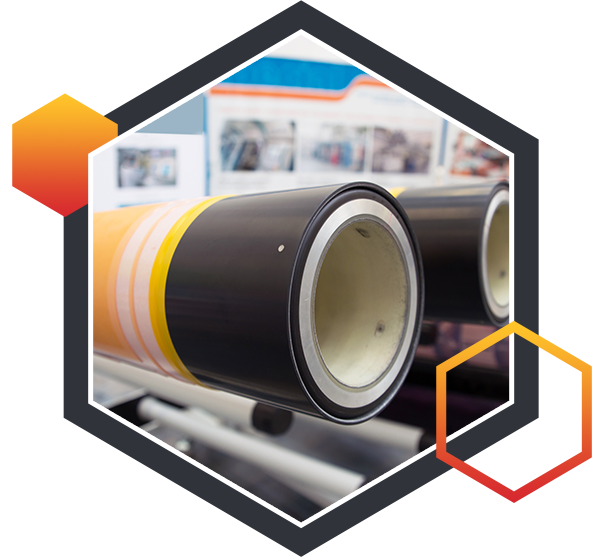
WHAT ARE SOME OF THE ADVANTAGES OF FLEXOGRAPHY PRINTING AT IMPRESSION LABEL?
- Fast Production and Turnaround Times
- Access to a Wide Variety of Inks Like Water-Based, Solvent-Based, and U.V.-Curable
- Print Large Volumes in Less Time
- More Affordable Than Other Product Label Printing Methods
- Flexography Printing at Impression Label is Environmentally Conscious
Give us a call today to start your flexography printing services!
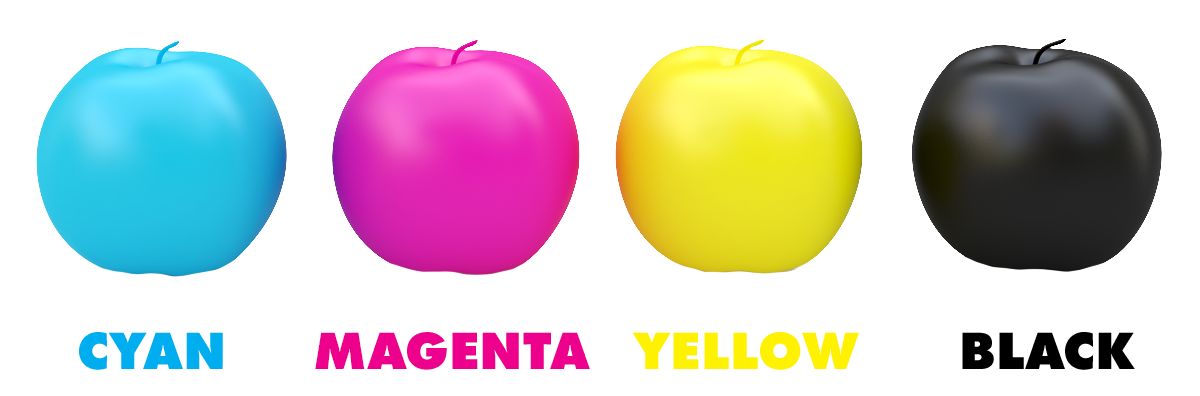
FLEXOGRAPHY PRINTING OVERVIEW
In the typical flexography printing sequence, the substrate is fed into the press from a roll. The image is printed as the substrate is pulled through a series of stations or print units. Each one prints a single color. As with Gravure and Lithographic printing, the various tones and shading are achieved by overlaying the four basic shades of ink: cyan, magenta, yellow, and black.
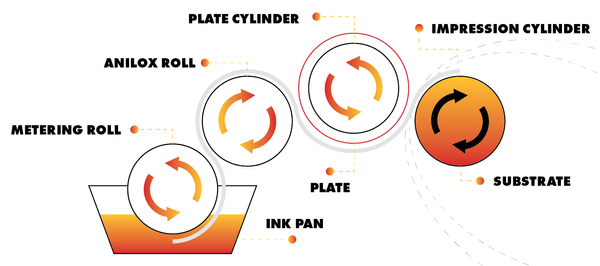
The process of printing each color on a flexo press consists of a series of four rollers:
- Ink Roller
- Meter Roller
- Plate Cylinder
- Impression Cylinder
The first roller transfers the ink from an ink pan to the meter roller, or Anilox Roll, which is the second roller. The Anilox roller meters the ink to a uniform thickness onto the plate cylinder to avoid bubbling or spots on the label. The substrate then moves between the plate cylinder and the impression cylinder, which is the fourth roller.
The impression cylinder applies pressure to the plate cylinder, thereby transferring the image onto the substrate. The web, which by now has been printed, is fed into the overhead dryer so the ink is dry before it goes to the next print unit.
After the substrate has been printed with all colors the web may be fed through an additional overhead tunnel dryer to remove most of the residual solvents or water. The finished product is then rewound onto a roll or is fed through the cutter.
LEARN MORE ABOUT HOW WE CAN HELP YOU!
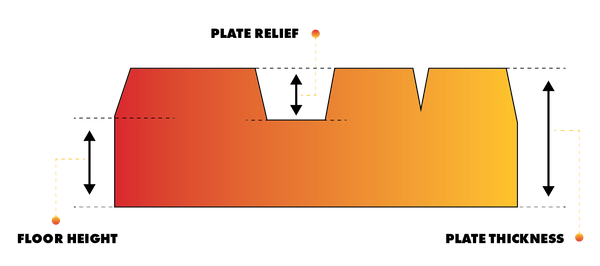
PLATE MAKING AND IMAGE PREP FOR FLEXOGRAPHY PRINTING
Plate making in flexography printing uses relief plates, which are unique to each label. However, prior to this is a rigorous set of procedures used to manipulate and generate images based on color processes. Plate-making utilizes a solid or liquid photopolymer that is exposed to light through a negative. Afterward, the desired areas left unexposed are then washed away with solvent or water to produce the plate relief and floor height, creating the plate thickness as the image demonstrates.
Image preparation in flexography printing begins with electronically produced art supplied by the customer, or we’ll create the art by providing you with two free hours of time from our professional art department. Images are captured for printing by a camera, scanner, or computer. When the art is scanned or digitally captured, the computer, which is equipped with special software, assembles the image. A simple proof is prepared to check for position and accuracy. When color is involved, a digital color proof is submitted to the customer for approval. Upon approval, our professional art department then prepares the image for plating on our NX System.
INKS
The inks used in flexography printing consist of colorants, which may be pigments and soluble dyes along with a binder and various solvents. Both solvent-based and water-based inks commonly contain various types of alcohol as the primary solvent or drier. Alcohol rapidly dries through evaporation and contributes to VOC emissions. The inks may also contain glycol ether and/or ammonia which facilitates drying.

U.V.-CURABLE
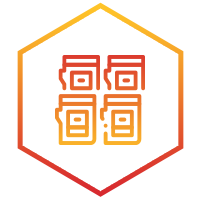
SOLVENT-BASED
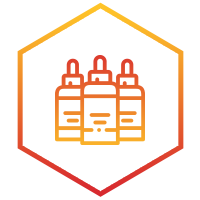
WATER-BASED
Water-based flexography inks dry through evaporation and absorption on paper. This evaporation requires a greater amount of energy to dry the ink. Coated papers may be used to control the absorption through the paper. Due to the speed of the presses and volume of inks consumed daily, a pollution control system may be necessary — especially if the printer is using solvent-based inks. If the product allows, the printer may avoid pollution control equipment if they convert to water-based inks or U.V.-curable inks.
The cost of pollution control equipment for a small flexography or gravure printer will cost approximately $400,000 (1998 estimate) for the equipment and approximately $50,000 for testing and certification. The price increases as the size and/or volume of the operation increases.
U.V. flexography inks are commonly used for topcoats and lacquers, and are responsible for improving image quality for flexographic printing. The use of U.V.-curable colored inks is rising within the flexographic printing industry, but product concerns and equipment investment are notable obstacles. It's also worth noting that water-based or U.V.-curable inks may not be an option for some printers due to the substrate being printed or designed.
PRINTING PRESSES
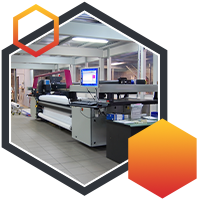
COMMERCIAL PUBLICATION FLEXOGRAPHIC PRESSES
Commercial publication flexographic presses are compact, high-speed presses with wide web capabilities that utilize dedicated four-, five-, or six-color units. Typically, two four-color units are paired in one press to allow printing on both sides of the web. Publication flexographic presses generally incorporate infrared dryers to ensure drying of the waterborne ink after each side of the web is printed (Buonicore).
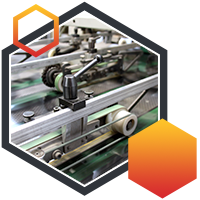
IN-LINE
In-Line flexography printing is similar to a unit type rotary press or the stacked press except the printing stations are arranged in a horizontal line. They are all driven by a common line shaft and may be coupled to folders, cutters, and other post-press equipment. These presses are used in label printing services for printing bags, corrugated board, folding boxes, and similar products.
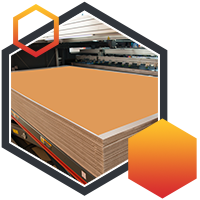
CENTRAL IMPRESSION CYLINDER (CIC)
Central impression cylinder (CIC), like the common impression rotary letterpress, uses a single impression cylinder mounted in the press frame. Two to eight color printing stations surround the central impression cylinder. Each station consists of an ink pan, fountain roller, anilox roll, doctor blade, and plate cylinder. As the web enters the press it comes into contact with the impression cylinder and remains in contact until it leaves the press. The result is precise registration which allows CIC presses to produce very good color impressions. CIC presses are used extensively in label printing services for flexible films.
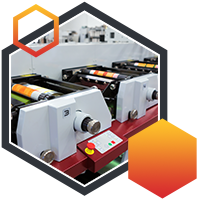
STACK TYPE
The stack press is characterized by one or more stacks of printing stations arranged vertically on either side of the press frame. Each stack has its own plate cylinder which prints one color of a multicolor impression. All stations are driven from a common gear train. Stack presses are easy to set up and can print both sides of the web in one pass. They can be integrated with winders, unwinders, cutters, creasers, and coating equipment. They are very popular in milk carton printing. A drawback of stack presses is their poor registration; the image position on every printed sheet is not as consistent as in many other product label printing processes.
APPLICATIONS
Flexography Printing is Used for the Production of:
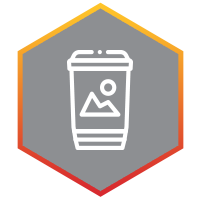
PACKAGING MATERIALS
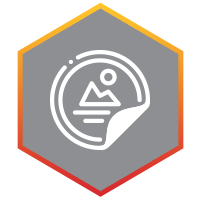
LABELS
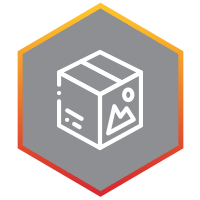
FOLDING CARTONS
Large quantities of inks are used during normal runs on flexographic presses; however, we are able to recycle a majority of our spent inks and wash waters.
Major chemicals used in flexography include plate-making solution, water and solvent-based inks, and blanket/roller cleaning solvents.
FINISHING
After printing, the substrate may run through a number of operations to be finished and ready for shipment to the customer. Finishing may include operations such as coating, cutting, folding, and binding.
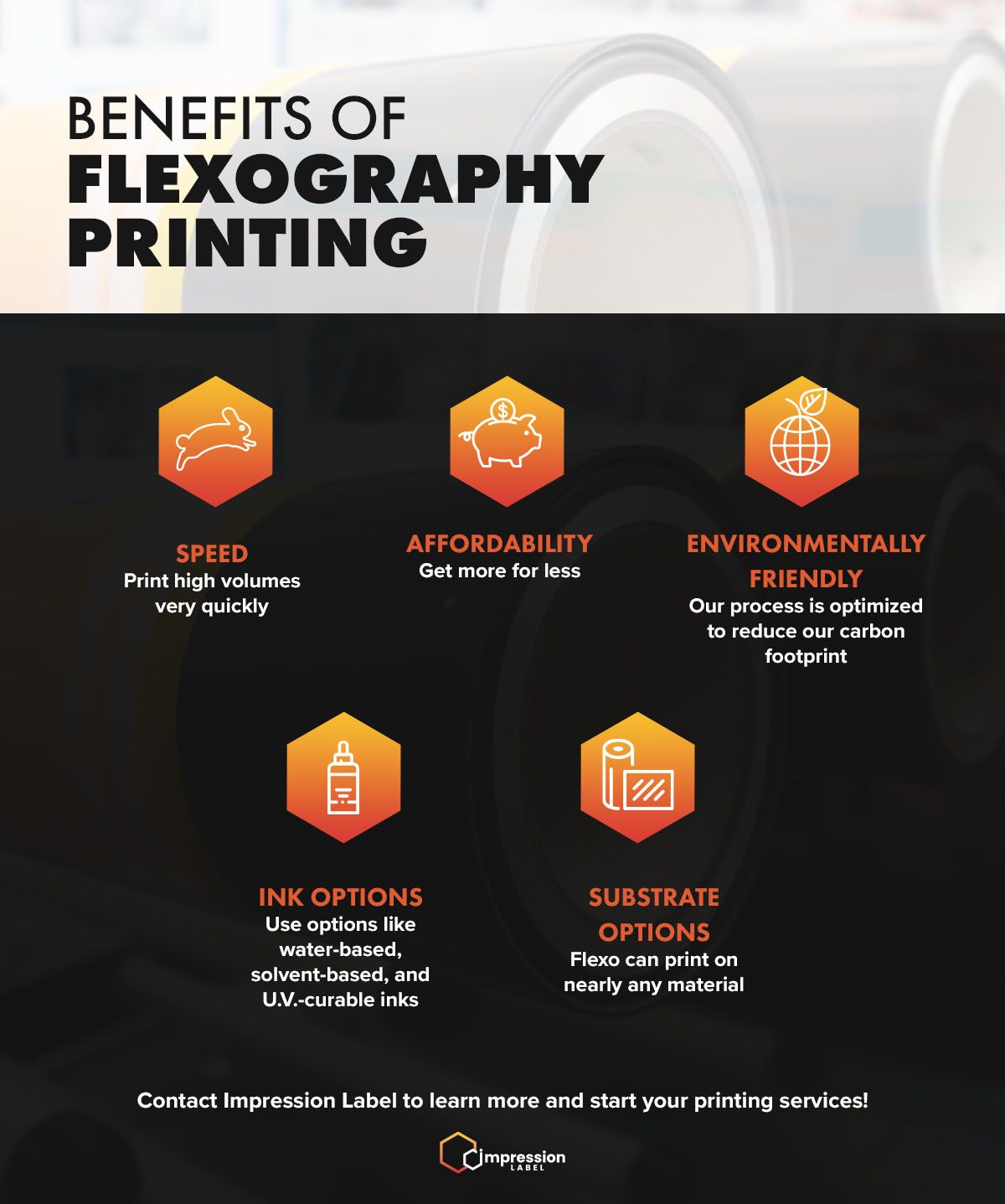