Flexography Printing 101
Flexography, often referred to as "flexo," is a dynamic and efficient printing method that has transformed the way businesses approach large-scale printing. At Impression Label, we rely on this innovative technology to provide high-quality, cost-effective solutions for our clients. This blog will serve as a detailed introduction to flexography, explaining its process, benefits, and why it has become the preferred printing method for various industries.
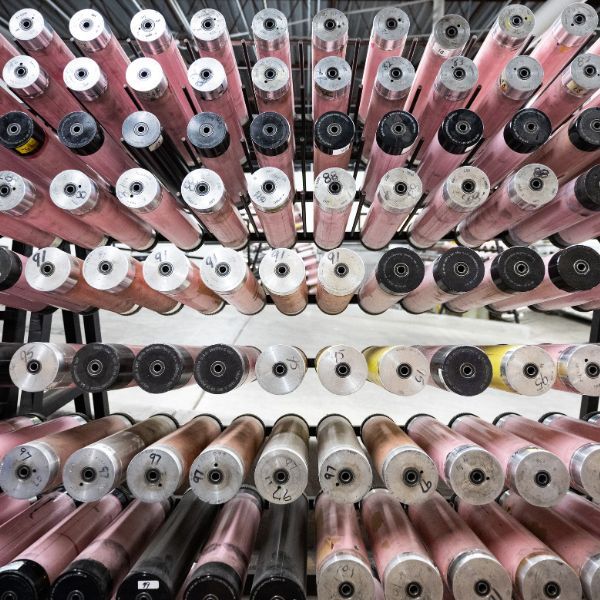
What Is Flexography?
Flexography is a modern, high-speed rotary printing method that uses flexible relief plates to transfer ink onto a surface, known as the substrate. Initially developed as a method for printing on uneven surfaces, flexography has evolved into a sophisticated and versatile printing process. Today, it is widely used in the packaging and labeling industries for its ability to handle diverse materials while maintaining high production speeds and exceptional quality.
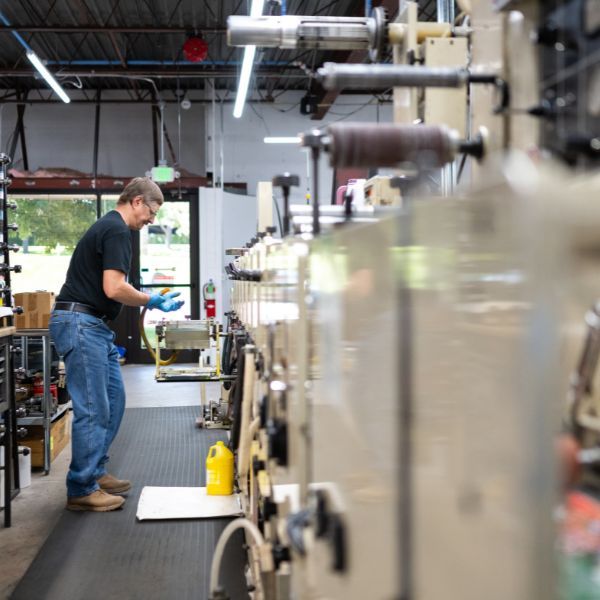
How Does Flexography Work?
The flexographic printing process begins with the substrate, typically supplied in roll form, being fed into the press. Each printing station contains a flexible relief plate that corresponds to a specific color. Here’s a breakdown of the process:
Ink Transfer: Ink is applied to an anilox roller, a specialized cylinder that ensures the correct amount of ink is evenly distributed.
Plate Contact: The inked anilox roller transfers ink onto the flexible plate, which is etched with the design.
Printing: The plate presses the ink onto the substrate as it passes through the machine. Each color requires its own plate and station, and the combined result produces a vibrant and accurate final image.
The ability to integrate additional processes, such as laminating or die-cutting, into a single pass adds to the efficiency of flexographic printing.
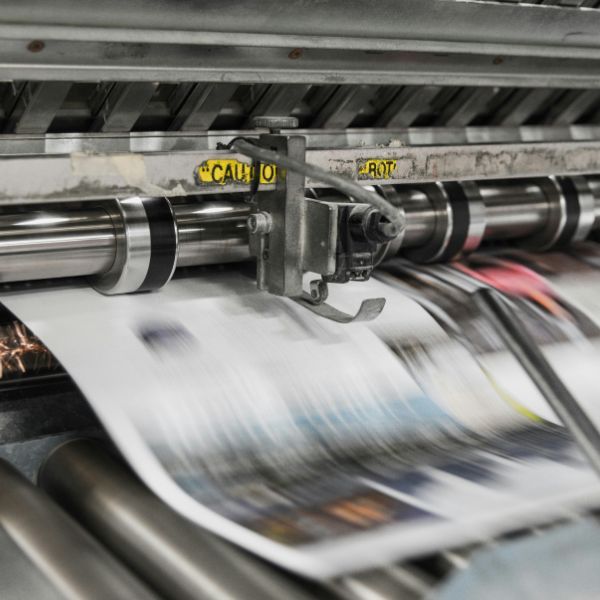
Materials Compatible with Flexography
Flexography’s versatility stems from its ability to print on a wide variety of substrates. This includes both absorbent and non-absorbent materials, such as:
Paper and cardboard, are used for packaging and labels.
Plastic films are ideal for food packaging and flexible pouches.
Metallic and non-woven surfaces offer unique applications for specialty products.
This adaptability makes flexography an attractive option for industries with diverse needs, from food and beverage to consumer goods.
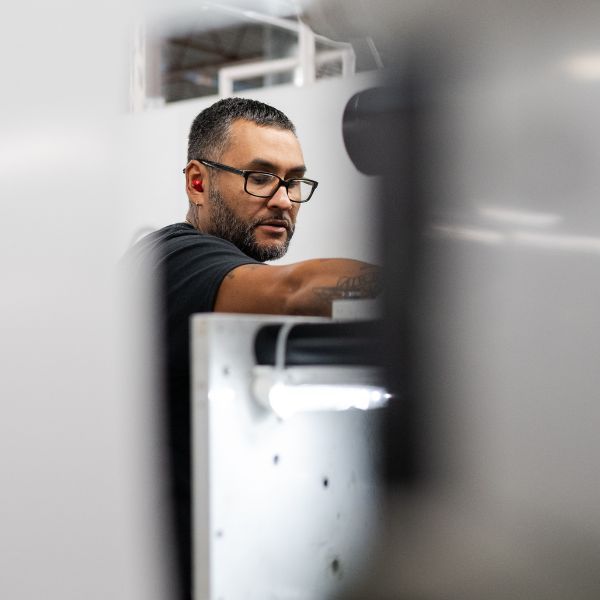
Applications of Flexographic Printing
Flexographic printing is known for its versatility and efficiency, making it the go-to method for high-volume printing in various industries. It produces durable, high-quality packaging, including food wrappers, corrugated boxes, and labels, offering self-adhesive and cut-and-stack options with vibrant colors. Retail bags, whether plastic or paper, are also well-served, as flexography seamlessly prints designs that support branding. Additionally, its scalability makes it ideal for manufacturing promotional materials and tags in large quantities while ensuring consistent quality.

Advantages of Flexographic Printing
Flexographic printing offers significant advantages over other methods, particularly in terms of speed and cost-effectiveness. Modern flexographic presses can quickly handle large volumes, reducing production time, while the durability and reusability of printing plates lower costs for long runs. This method is versatile, printing on various substrates, including porous paper and non-porous plastic films. Additionally, flexography is environmentally friendly, using water-based and UV-cured inks that reduce environmental impact. These features make it a reliable choice for businesses seeking high-quality, scalable printing solutions.
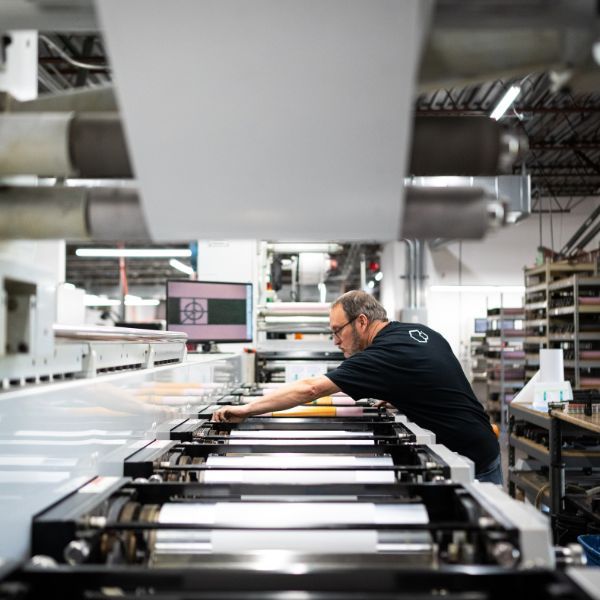
How Flexography Compares to Other Printing Methods
Compared to offset and digital printing, flexography offers distinct advantages:
Direct Printing: Unlike offset printing, which requires intermediary steps, flexography prints directly onto the substrate.
Integration: Additional steps such as laminating and die-cutting can be incorporated into a single production pass.
Material Range: While offset printing is limited to smooth, flat surfaces, flexography excels on textured or irregular materials.
These features make flexography particularly appealing for businesses requiring diverse and scalable printing solutions.
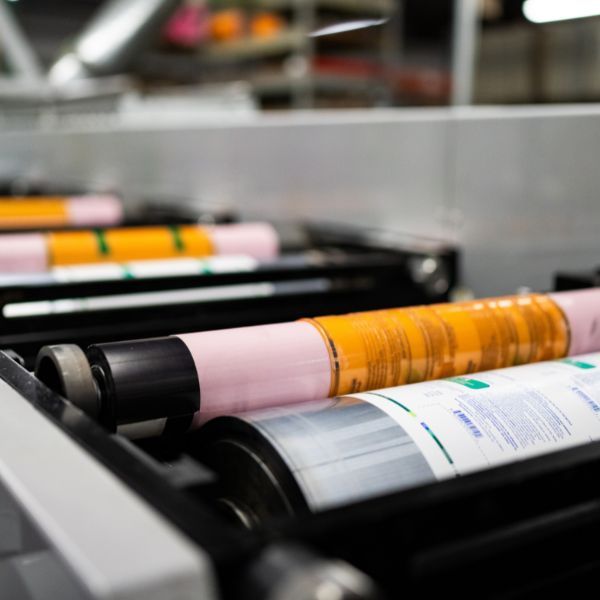
The Role of Inks in Flexography
The choice of ink is critical to the success of any printing method, and flexography excels in this regard.
Water-Based Inks: Ideal for eco-conscious printing, offering excellent results on porous materials.
Solvent-Based Inks: Provide durability and adhesion for non-porous substrates.
UV-Curable Inks: These inks cure instantly when exposed to ultraviolet light, speeding up production and improving image quality.
UV inks are increasingly popular for their vibrant colors, reduced drying times, and absence of volatile organic compounds (VOCs).
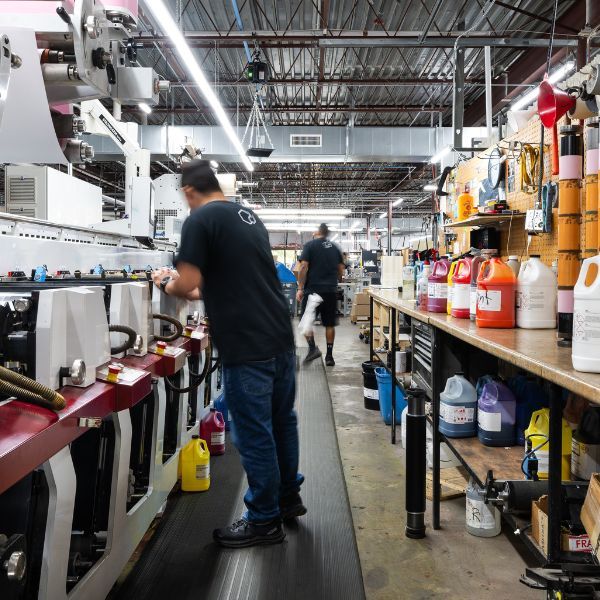
Emerging Trends in Flexography
Flexography continues to evolve with advancements in technology. High-definition flexographic plates and automated press controls are improving image resolution and reducing waste. The incorporation of AI and digital monitoring ensures greater consistency and fewer errors. These innovations are helping flexography remain competitive in a rapidly changing industry.
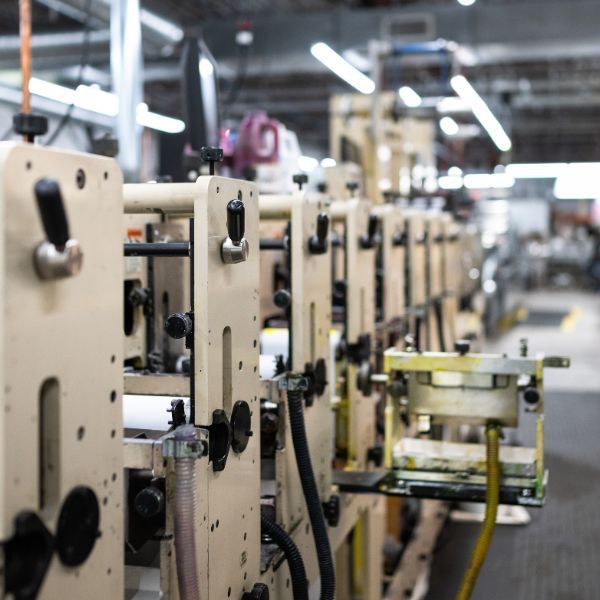
Quality Control in Flexography
Ensuring the quality of printed products is essential for businesses that rely on flexography. Advanced monitoring systems, such as inline inspection cameras, help ensure that the final output matches the desired quality standards. Regular calibration of the press, ink formulation, and substrate is essential to prevent color inconsistencies or defects during the printing process. We prioritize quality control to deliver flawless, high-quality prints every time.
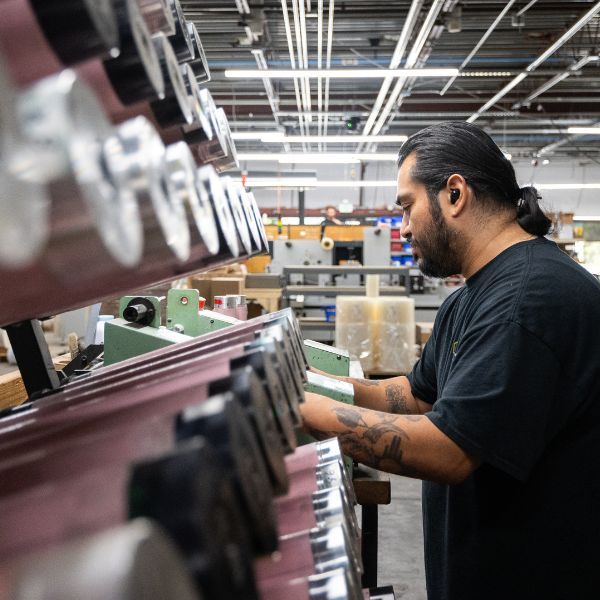
Flexography at Impression Label
At Impression Label, we leverage flexography’s unique benefits to provide clients with exceptional printing services. Our state-of-the-art equipment and skilled technicians enable us to handle projects of any size with speed and precision. Whether you need labels, packaging, or promotional materials, our team ensures a seamless production process from start to finish.
Flexography is an innovative and highly versatile printing method that offers significant advantages in speed, cost, and quality. Its ability to print on a variety of substrates and integrate additional processes makes it the ideal choice for businesses that require efficient, high-volume printing.
At Impression Label, we are proud to offer flexographic printing as part of our comprehensive label and packaging solutions. Contact us today to learn more about how we can meet your printing needs with our advanced flexography solutions.